Aluminium Casting Dies Precision and Efficiency in Manufacturing
In the realm of manufacturing, aluminium casting dies play a pivotal role. These precision tools are designed to transform molten aluminium into intricate shapes and components for a wide range of applications. The process of aluminium casting involves pouring molten metal into a die, where it solidifies under controlled conditions to achieve the desired shape and size. The quality and performance of these castings are heavily influenced by the design and construction of the casting die.
The design of an aluminium casting die is a complex task that requires a deep understanding of the material properties, casting process, and product requirements. Engineers must consider factors such as shrinkage, warping, and draft angles to ensure that the castings will emerge from the die without defects. The die material must also be chosen carefully, as it must withstand the high temperatures and pressures involved in the casting process without deforming or wearing out.
One of the key advantages of aluminium casting dies is their ability to produce complex shapes and components with relative ease. Unlike other casting processes, such as sand casting, which can be limited by the complexity of the mould, aluminium casting dies can accommodate intricate designs with relative precision. This makes them ideal for producing parts for industries such as automotive, aerospace, and consumer electronics, where lightweight and complex structures are paramount This makes them ideal for producing parts for industries such as automotive, aerospace, and consumer electronics, where lightweight and complex structures are paramount
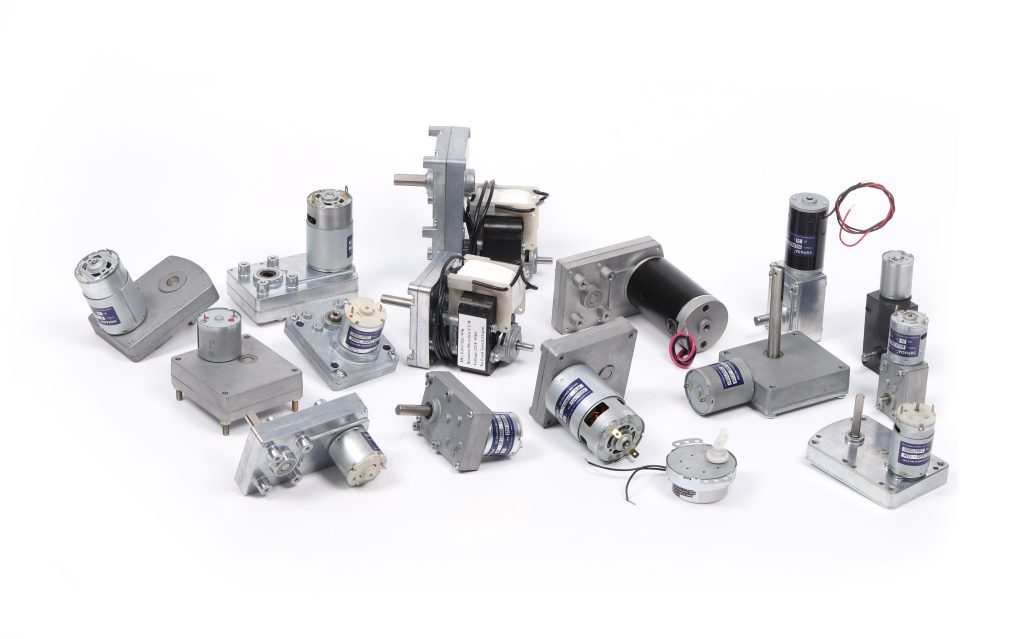
This makes them ideal for producing parts for industries such as automotive, aerospace, and consumer electronics, where lightweight and complex structures are paramount This makes them ideal for producing parts for industries such as automotive, aerospace, and consumer electronics, where lightweight and complex structures are paramount
aluminium casting die.
Another significant advantage of aluminium casting dies is their efficiency. Once a die has been designed and manufactured, it can be used repeatedly to produce large numbers of castings with minimal downtime. This makes them a cost-effective solution for high-volume production runs. Moreover, the use of aluminium casting dies can also lead to significant energy savings compared to other casting processes, as they require less heat and pressure to achieve the same results.
In conclusion, aluminium casting dies are essential tools in the manufacturing industry, offering precision, efficiency, and versatility in the production of complex components. As demand for lightweight and high-performance materials continues to grow, the importance of these tools is likely to increase in the years ahead. With continued advancements in design and materials technology, we can expect to see even more sophisticated and efficient aluminium casting dies being developed to meet the ever-evolving needs of manufacturers around the world.