Globe Valve Casting A Comprehensive Guide
Globe valves are a crucial component in various industrial processes, including chemical processing, water treatment, and power generation. These valves are designed to control the flow of fluids by opening, closing, or partially obstructing a passageway. The casting process is a critical step in manufacturing globe valves, as it determines the quality, strength, and durability of the final product. In this article, we will delve into the process of globe valve casting and its importance in the production of these vital components.
Casting is a manufacturing process that involves pouring molten metal into a mold and allowing it to solidify. The mold is typically made of sand, ceramic, or another material that can withstand the high temperatures of molten metal. Globe valve casting involves creating a mold that resembles the internal and external geometry of the valve, including the valve body, bonnet, and disc.
The casting process for globe valves begins with the preparation of the mold. This involves creating a pattern, which is a replica of the valve that will be cast. The pattern is made using materials such as wood, plastic, or metal and is used to create the mold cavities. Once the pattern is complete, it is placed into a flask, which is a container used to hold the sand or other molding material.
The molding material is then packed around the pattern to create the mold cavities. The mold is then cured, which involves allowing the molding material to harden and solidify. Once the mold is fully cured, it is removed from the flask and the pattern is extracted Once the mold is fully cured, it is removed from the flask and the pattern is extracted
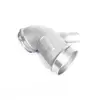
Once the mold is fully cured, it is removed from the flask and the pattern is extracted Once the mold is fully cured, it is removed from the flask and the pattern is extracted
globe valve casting. The mold is then ready for use in the casting process.
During the casting process, molten metal is poured into the mold cavities. The metal is allowed to cool and solidify, forming the final shape of the valve. After the metal has solidified, the mold is broken apart to reveal the finished valve. The valve is then cleaned, inspected, and tested to ensure that it meets the required specifications.
The casting process offers several advantages when it comes to manufacturing globe valves. One of the main benefits is cost-effectiveness. Casting allows manufacturers to produce large quantities of valves at a lower cost than other manufacturing methods, such as machining. Additionally, casting allows for greater design flexibility, as the mold can be easily modified to accommodate different valve sizes and designs.
In conclusion, globe valve casting is a critical process in the manufacturing of these vital components. By following best practices and utilizing advanced technologies, manufacturers can produce high-quality globe valves that meet the demanding requirements of various industries. With its cost-effectiveness, design flexibility, and ability to produce large quantities of valves, casting remains an essential manufacturing method for globe valves.