Stainless steel valve casting is a pivotal component in various industries, including oil and gas, chemical, power generation, and water treatment. The intricate process of creating these valves involves precision, expertise, and a thorough understanding of materials and procedures to ensure quality, durability, and performance.
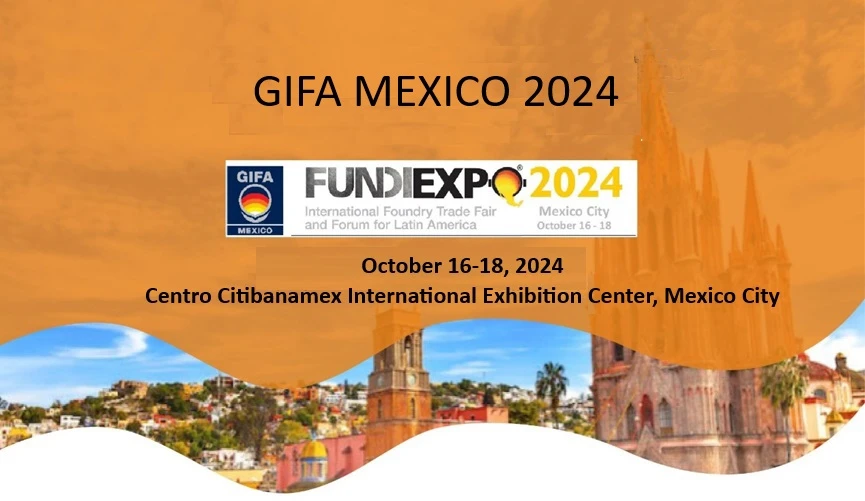
At the heart of the stainless steel valve casting process is the selection of appropriate materials. Stainless steel is favored due to its resistance to corrosion, high temperature, and pressure endurance capabilities. The specific type of stainless steel used can vary depending on the end application, with common variants being 304, 316, and 316L. Each type possesses its unique properties making it suitable for different environments and mechanical stresses.
The casting process begins with the creation of a precise mold, often achieved through investment casting, due to its ability to produce intricate designs and maintain tight tolerances. This method involves creating a wax model of the valve, which is then encased in a ceramic shell. After the shell hardens, the wax is melted and drained away, leaving a cavity in the shape of the valve.
Molten stainless steel is then poured into this cavity. Once solidified, the ceramic shell is broken away to reveal the cast valve.
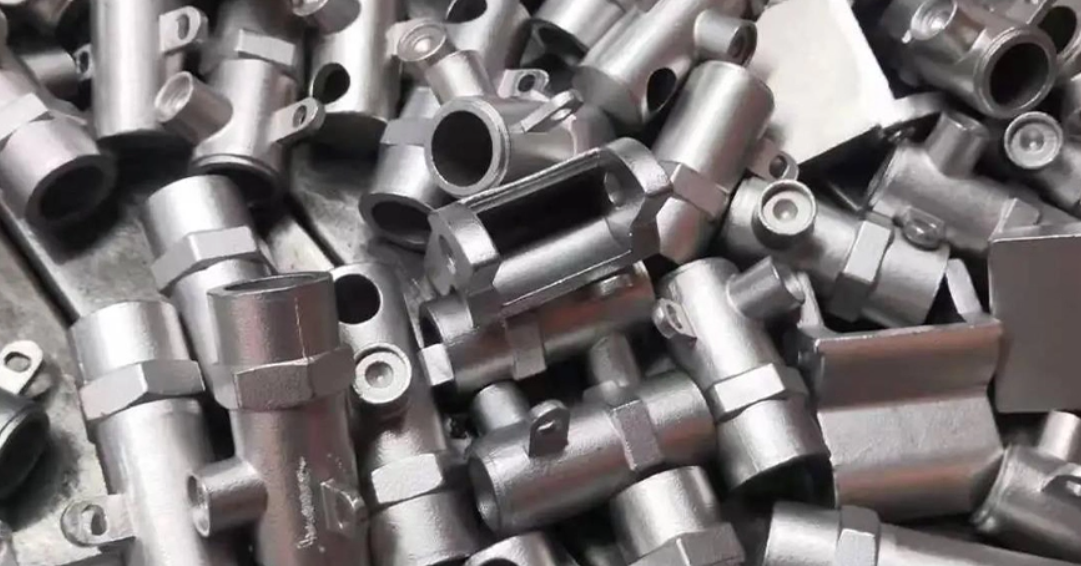
Precision in casting is crucial. Improper casting can lead to defects such as porosity, shrinkage, and misalignment, which can compromise the integrity and functionality of the valve. Manufacturers combat these issues by employing advanced simulation software to predict the behavior of the molten metal and refine the mold designs accordingly.
Ensuring quality doesn't stop at the casting process. Post-casting operations are equally critical. These include heat treatment to enhance mechanical properties, machining to achieve exact dimensions, and a rigorous inspection process that involves both non-destructive and destructive testing. Non-destructive testing methods, such as ultrasonic, radiographic, or dye penetrant, ensure there are no internal defects or surface flaws. Destructive testing may be used in some scenarios to achieve certifications and compliance with industry standards.
stainless steel valve casting
Accredited manufacturers adhere strictly to international standards, such as with the American Society of Mechanical Engineers (ASME) or the International Organization for Standardization (ISO). These standards guide production, ensuring that the final products meet the necessary safety and performance metrics. Companies that align with these regulations demonstrate a level of authority and trustworthiness, assuring clients of their commitment to quality and reliability.
Choosing the right stainless steel valve manufacturer involves considering their experience and expertise in the field. Established manufacturers often have decades of experience, contributing valuable insights and reliability in product performance. They invest in cutting-edge technology and skilled personnel to maintain their competitive edge in a growing market.
Moreover, environmental considerations are increasingly influencing production methods. Sustainable practices such as recycling stainless steel and reducing carbon emissions are becoming standard. Manufacturers with a focus on sustainability can offer clients not just a product, but a part of a conscientious supply chain that aligns with contemporary corporate and consumer values.
In a world that demands dependability and performance from every industrial component, stainless steel valve casting offers unmatched assurance. Through a blend of expert material selection, advanced manufacturing techniques, and unwavering commitment to quality standards, these components stand as pillars of industrial infrastructure.