Low Pressure Aluminum Casting An Innovative Manufacturing Technique
Low Pressure Aluminum Casting is an advanced manufacturing process that has revolutionized the metal casting industry, particularly in the production of high-quality aluminum components. This technique involves filling a mold with molten aluminum under controlled low pressure, offering a myriad of benefits over traditional casting methods.
The process begins with the aluminum alloy being heated to its melting point in a holding furnace. The molten metal is then fed into a pressure chamber located beneath the mold cavity. As the name suggests, a low pressure is applied to push the liquid aluminum upwards through a riser tube into the mold. This slow and steady flow ensures a uniform filling of the mold, minimizing entrapped air and reducing the formation of defects such as porosity.
One of the key advantages of low pressure aluminum casting is its ability to produce parts with exceptional dimensional accuracy and surface finish. The controlled filling under low pressure results in less shrinkage and less distortion, leading to components with superior mechanical properties. This makes it ideal for manufacturing intricate and complex shapes, which would be challenging or impossible to achieve using other casting techniques.
Moreover, this method allows for better utilization of the metal, reducing waste and lowering costs
Moreover, this method allows for better utilization of the metal, reducing waste and lowering costs
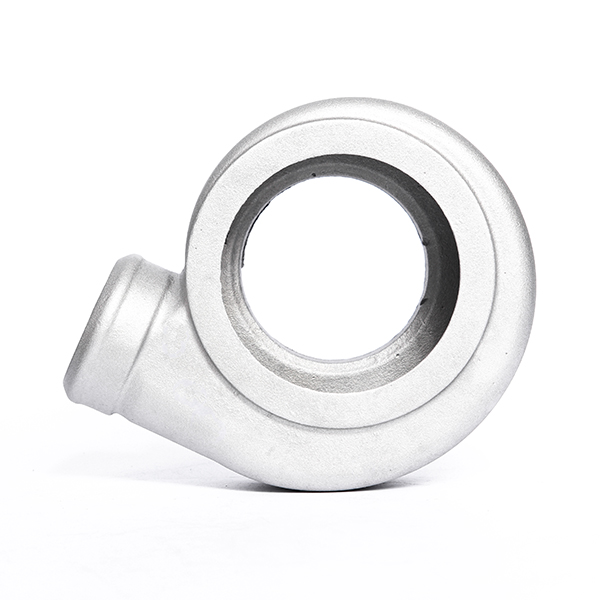
Moreover, this method allows for better utilization of the metal, reducing waste and lowering costs
Moreover, this method allows for better utilization of the metal, reducing waste and lowering costs
low pressure aluminum casting. The low-pressure environment also promotes a more consistent and reliable quality, making it suitable for industries where precision and repeatability are paramount, such as automotive, aerospace, and electronics.
Despite its numerous benefits, low pressure aluminum casting requires precise control and monitoring of parameters like pressure, temperature, and fill time. It demands skilled operators and sophisticated equipment, which can increase initial investment costs. However, the long-term savings in material usage, reduced post-processing, and enhanced product quality often outweigh these upfront expenses.
In conclusion, low pressure aluminum casting is a game-changing technology that offers a blend of precision, efficiency, and cost-effectiveness. It not only enhances the overall performance of aluminum components but also paves the way for more sustainable manufacturing practices. As technology continues to evolve, we can expect low pressure aluminum casting to play an even larger role in shaping the future of metal casting industry.