The Role of Vortex Casing in Centrifugal Pumps
In the domain of fluid dynamics, the centrifugal pump stands as a cornerstone for industrial and agricultural applications. A vital component that enhances its efficiency is the vortex casing, which plays a pivotal role in the pump's performance. This article delves into the significance of the vortex casing within a centrifugal pump, highlighting its design and functional benefits.
The vortex casing, true to its name, is designed with a spiral shape resembling a whirlpool or vortex. This unique configuration optimizes the flow of liquid by minimizing energy losses and maintaining a consistent velocity as the fluid travels from the pump's eye to its discharge. Unlike conventional casings, the vortex design reduces turbulence, leading to a smoother transition for the fluid, thereby conserving kinetic energy.
The operational principle of a centrifugal pump hinges on the conversion of kinetic energy to potential energy. As the pump's impeller rotates, it propels the fluid outward, where it encounters the vortex casing. This casing's structure ensures that the fluid's velocity is gradually reduced as it moves towards the pump's exit, preventing energy dissipation and reducing the risk of backflow.
Moreover, the vortex casing contributes to noise reduction within the pumping system
Moreover, the vortex casing contributes to noise reduction within the pumping system
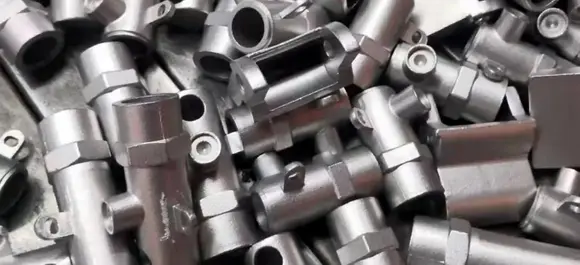
Moreover, the vortex casing contributes to noise reduction within the pumping system
Moreover, the vortex casing contributes to noise reduction within the pumping system
vortex casing in centrifugal pump. By streamlining the fluid flow, it diminishes the impact and cavitation sounds typically associated with turbulent flow conditions. This not only makes the pump operation quieter but also indicates a smoother running process, which can prolong the pump's service life.
In terms of efficiency, the vortex casing's design allows for a more precise matching of the pump's performance curve to the system's requirements. This tailored approach ensures that the pump operates at its best efficiency point (BEP) more frequently, translating into optimized energy usage and cost savings for the end-user.
In conclusion, the integration of a vortex casing in a centrifugal pump is not merely an aesthetic choice but a testament to engineering ingenuity aimed at enhancing efficiency, reducing operational noise, and extending equipment lifespan. Its swirling contours are emblematic of the continuous advancements in pump technology, reflecting our quest for improved fluid handling solutions. As we look to the future, the refinement of such components will undoubtedly continue to drive the efficacy of centrifugal pumps in diverse environments, underscoring their adaptability and indispensable nature across various sectors.