Custom Stainless Steel Casting A Tailored Approach to Metalworking
In the realm of metallurgy, custom stainless steel casting stands as a testament to human ingenuity and precision. This specialized process involves creating bespoke stainless steel components that are designed to meet specific requirements, transcending the limitations of standardized parts. The alloy's resistance to corrosion, along with its strength and durability, makes it an ideal choice for industries ranging from automotive and aerospace to architecture and medical equipment.
The journey of custom stainless steel casting begins with a detailed blueprint or computer-aided design (CAD) model. These plans are meticulously crafted to reflect the exact dimensions, tolerances, and performance expectations of the end product. From here, the process diverges into various paths depending on the complexity of the part and the quantity needed. For one-off or small-volume production, investment casting is often preferred due to its ability to reproduce intricate details and fine finishes.
The heart of the operation is the foundry, where molten stainless steel is poured into precise molds created from the aforementioned models. The molds are typically made from refractory materials that can withstand the high temperatures involved in the casting process. Once the steel has solidified and cooled, the mold is carefully removed to reveal the cast part. However, this is just the beginning.
Post-casting, the part undergoes a series of finishing processes to ensure it meets the desired specifications. This may involve sandblasting to remove any residual mold material, cutting and grinding to achieve precise dimensions, and polishing for a smooth finish This may involve sandblasting to remove any residual mold material, cutting and grinding to achieve precise dimensions, and polishing for a smooth finish
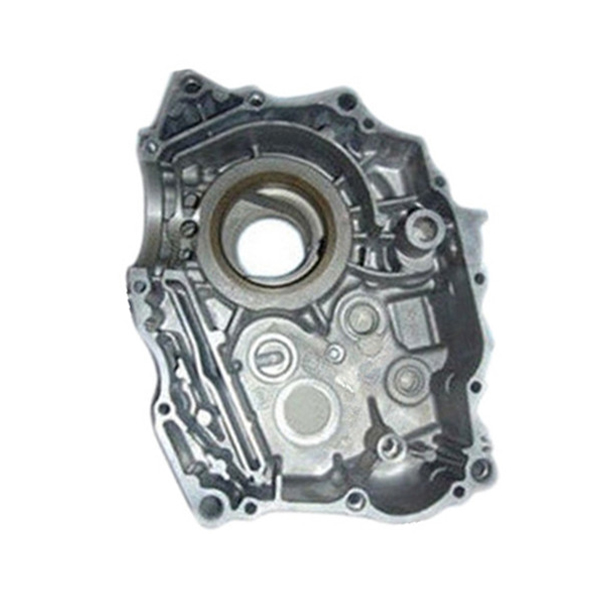
This may involve sandblasting to remove any residual mold material, cutting and grinding to achieve precise dimensions, and polishing for a smooth finish This may involve sandblasting to remove any residual mold material, cutting and grinding to achieve precise dimensions, and polishing for a smooth finish
custom stainless steel casting. Quality control checks are integral throughout these stages, ensuring that each component adheres strictly to the agreed-upon standards.
One of the paramount benefits of custom stainless steel casting is its adaptability. Whether it's a large architectural feature requiring seamless integration or a critical component for a spacecraft demanding uncompromising accuracy, this method delivers. It allows for the creation of complex geometries that would otherwise be impossible to achieve through standard manufacturing techniques.
Moreover, custom stainless steel casting offers a sustainable solution. By producing only what is necessary, waste is minimized, and resources are used efficiently. The longevity of stainless steel components further enhances sustainability by reducing the need for replacements and decreasing maintenance costs over time.
In conclusion, custom stainless steel casting is more than just a manufacturing process; it is an art form where science and creativity converge. Its ability to produce tailored solutions that meet unique demands has made it an indispensable tool across diverse sectors. As technology continues to advance, so too will the capabilities of custom stainless steel casting, ensuring it remains at the forefront of metallurgical innovation.