Aluminum Gravity Casting A Revolutionary Approach to Metal Fabrication
In the realm of metal fabrication, aluminum gravity casting stands as a testament to the ingenuity and innovation that permeate the industry. This process, characterized by its simplicity and efficiency, has revolutionized the way in which aluminum alloys are shaped into intricate forms for various applications.
At its core, aluminum gravity casting relies on the fundamental force of gravity to facilitate the flow of molten aluminum into a pre-prepared mold cavity. Unlike pressure casting or other complex processes, it does away with the need for high-pressure machinery, making it a cost-effective and accessible method for producing high-quality castings.
The procedure begins with the careful preparation of an aluminum alloy suitable for casting. Once the alloy is melted to the appropriate temperature, it is then poured into a furnace that holds it at a steady state. The molten metal is subsequently allowed to descend through a downsprue and into the cavity of a meticulously crafted mold. This mold, often made from materials such as steel or iron, is designed to withstand the heat and has a precise internal geometry to shape the final product.
One of the key advantages of aluminum gravity casting is its ability to produce parts with a fine surface finish and tight dimensional tolerances. The slow, controlled filling of the mold ensures that the metal cools uniformly, minimizing defects such as porosity, shrinkage, and gas entrapment The slow, controlled filling of the mold ensures that the metal cools uniformly, minimizing defects such as porosity, shrinkage, and gas entrapment
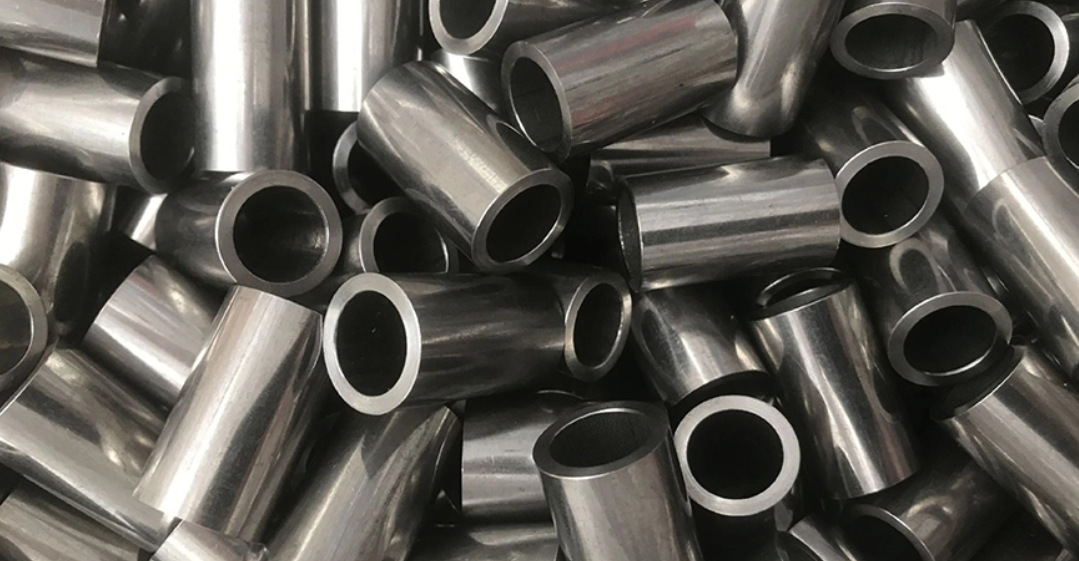
The slow, controlled filling of the mold ensures that the metal cools uniformly, minimizing defects such as porosity, shrinkage, and gas entrapment The slow, controlled filling of the mold ensures that the metal cools uniformly, minimizing defects such as porosity, shrinkage, and gas entrapment
aluminum gravity casting. Moreover, this method allows for the inclusion of intricate details and undercuts in the design, features that might be challenging to achieve with other casting techniques.
As the molten aluminum fills the mold, it gradually solidifies, taking on the negative space of the cavity. Once cooled and solidified, the casting is removed from the mold, revealing a part that is ready for further processing such as trimming, sanding, or machining to reach its final specifications.
The versatility of aluminum gravity casting makes it an ideal choice for a wide array of industries. From automotive components and electrical enclosures to architectural elements and aerospace fittings, the products created through this method are both robust and visually striking.
In conclusion, aluminum gravity casting represents a significant milestone in the evolution of metalworking practices. Its combination of affordability, adaptability, and quality outcomes ensures its continued prominence within the manufacturing landscape. As technology advances and the demand for aluminum products grows, the importance of mastering and refining this casting technique will only become more evident, heralding a future where innovation and craftsmanship converge to create objects of function and beauty.