Aluminum Die Casting Foundry A Revolution in Manufacturing
The advent of aluminum die casting foundries has revolutionized the manufacturing industry, offering unparalleled precision, efficiency, and cost-effectiveness. This advanced technique involves injecting molten aluminum into a steel mold or die under high pressure, resulting in intricately shaped components with exceptional accuracy and consistency.
One of the most significant advantages of aluminum die casting is its ability to produce complex geometries that would be difficult or impossible to achieve through other manufacturing methods. The process allows for tight tolerances and fine details, making it ideal for creating small parts with precise dimensions. Moreover, the use of aluminum as the primary material offers several benefits, including its lightweight nature, excellent strength-to-weight ratio, and corrosion resistance.
In an aluminum die casting foundry, the production process begins with designing and fabricating the die, which is a crucial step that determines the quality and functionality of the final product. Once the die is ready, the molten aluminum is poured into the shot chamber of the die casting machine. The machine then applies high pressure to force the molten metal into the die cavity, where it cools and solidifies rapidly. After the part has cooled sufficiently, it is ejected from the die, and any excess material is trimmed away.
Aluminum die casting foundries have become essential in various industries, including automotive, aerospace, electronics, and consumer goods
Aluminum die casting foundries have become essential in various industries, including automotive, aerospace, electronics, and consumer goods
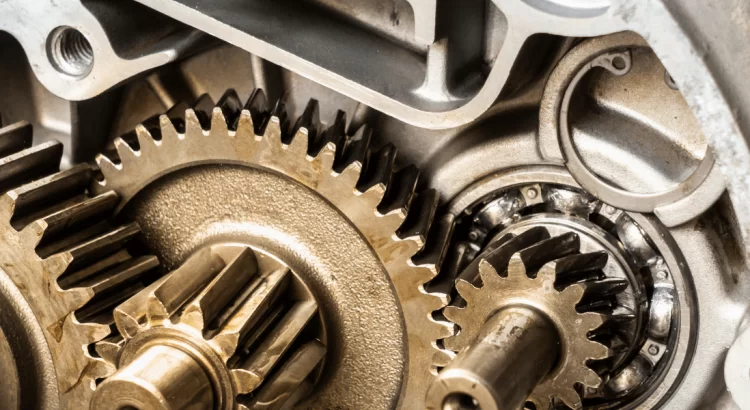
Aluminum die casting foundries have become essential in various industries, including automotive, aerospace, electronics, and consumer goods
Aluminum die casting foundries have become essential in various industries, including automotive, aerospace, electronics, and consumer goods
aluminum die casting foundry. Automotive manufacturers rely on this technology to produce lightweight yet sturdy engine components, chassis parts, and transmission cases. In the aerospace industry, die casting enables the creation of complex airframe structures and engine parts that require minimal weight while maintaining maximum strength.
Despite its numerous advantages, aluminum die casting faces challenges such as tooling costs and limitations in producing very large parts due to the size constraints of die casting machines. However, ongoing advancements in machinery, materials science, and process optimization continue to expand the capabilities of aluminum die casting foundries.
In conclusion, aluminum die casting foundries represent a pinnacle of modern manufacturing technology, offering unparalleled precision and efficiency in producing high-quality aluminum components. As demand for lightweight, strong, and intricately designed products continues to grow across various sectors, the importance of these foundries will only increase. With ongoing innovations in both process and materials, aluminum die casting remains at the forefront of industrial progress, shaping the future of manufacturing for years to come.