Aluminum Centrifugal Casting A Comprehensive Guide
Centrifugal casting is a versatile metal casting process that utilizes centrifugal force to produce complex shapes and intricate internal structures in aluminum castings. This method offers several advantages over other casting techniques, making it particularly suitable for high-volume production runs of components with precise dimensions and surface finishes.
The centrifugal casting process involves pouring molten aluminum into a rotating mold. As the mold rotates at high speeds, the centrifugal force generated pushes the molten metal towards the outer walls of the mold, where it solidifies under controlled conditions. This results in a casting with a uniform wall thickness and a smooth surface finish.
One of the key benefits of centrifugal casting is its ability to produce castings with intricate internal structures. By controlling the rotation speed and other process parameters, manufacturers can create castings with channels, ribs, and other features that would be difficult or impossible to achieve using other casting methods. This makes centrifugal casting an ideal choice for producing components such as engine blocks, impellers, and gears.
Another advantage of centrifugal casting is its ability to produce castings with excellent dimensional accuracy and surface finish
Another advantage of centrifugal casting is its ability to produce castings with excellent dimensional accuracy and surface finish
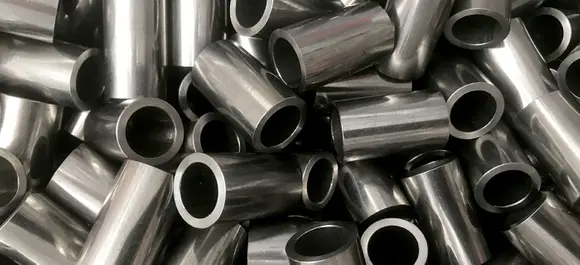
Another advantage of centrifugal casting is its ability to produce castings with excellent dimensional accuracy and surface finish
Another advantage of centrifugal casting is its ability to produce castings with excellent dimensional accuracy and surface finish
aluminum centrifugal casting. The centrifugal force ensures that the molten metal is distributed evenly throughout the mold, resulting in a casting with consistent dimensions and a smooth surface. This is particularly important for components that require tight tolerances or a high-quality finish.
Centrifugal casting also offers cost savings compared to other casting techniques. The process requires less machining and finishing, which reduces production costs and leads to faster turnaround times. Additionally, the use of reusable molds can further reduce costs by eliminating the need for expensive tooling.
In conclusion, aluminum centrifugal casting is a versatile and cost-effective metal casting process that produces high-quality castings with complex shapes and intricate internal structures. Its ability to produce castings with excellent dimensional accuracy and surface finish, combined with its cost savings, make it an attractive option for a wide range of applications.