Aluminum Bronze Casting A Revolutionary Material in Industrial Applications
Aluminum bronze, an alloy composed primarily of copper, aluminum, and iron, with minor additions of nickel, manganese, and other elements, has become a cornerstone in modern industrial casting. This unique blend of metals offers a plethora of benefits that make it exceptionally suitable for various applications where strength, durability, and resistance to corrosion are paramount. The process of aluminium bronze casting is both an art and a science, requiring precise control over the composition and solidification of the alloy to achieve the desired properties.
One of the most notable attributes of aluminium bronze is its high mechanical strength, even at elevated temperatures. This characteristic makes it ideal for components such as gears, valves, and propellers, which are constantly subjected to extreme stresses and heat. Moreover, the alloy's excellent wear resistance ensures that these parts maintain their integrity over prolonged periods, reducing maintenance costs and downtime.
The marine industry, in particular, has been a significant beneficiary of aluminium bronze casting. The alloy's combination of strength and resistance to saltwater corrosion is unparalleled, making it perfect for ship propellers. These propellers can endure the harsh marine environment while maintaining their efficiency and structural integrity, often outlasting competitors made from other materials.
Another area where aluminium bronze shines is in its application within heavy-duty machinery. Its natural frictional characteristics make it an excellent material for bearings and bushings that must endure high loads and operate smoothly under pressure. Additionally, the alloy's resistance to fatigue means that components cast from aluminium bronze can withstand repetitive stress cycles without cracking or failing Additionally, the alloy's resistance to fatigue means that components cast from aluminium bronze can withstand repetitive stress cycles without cracking or failing
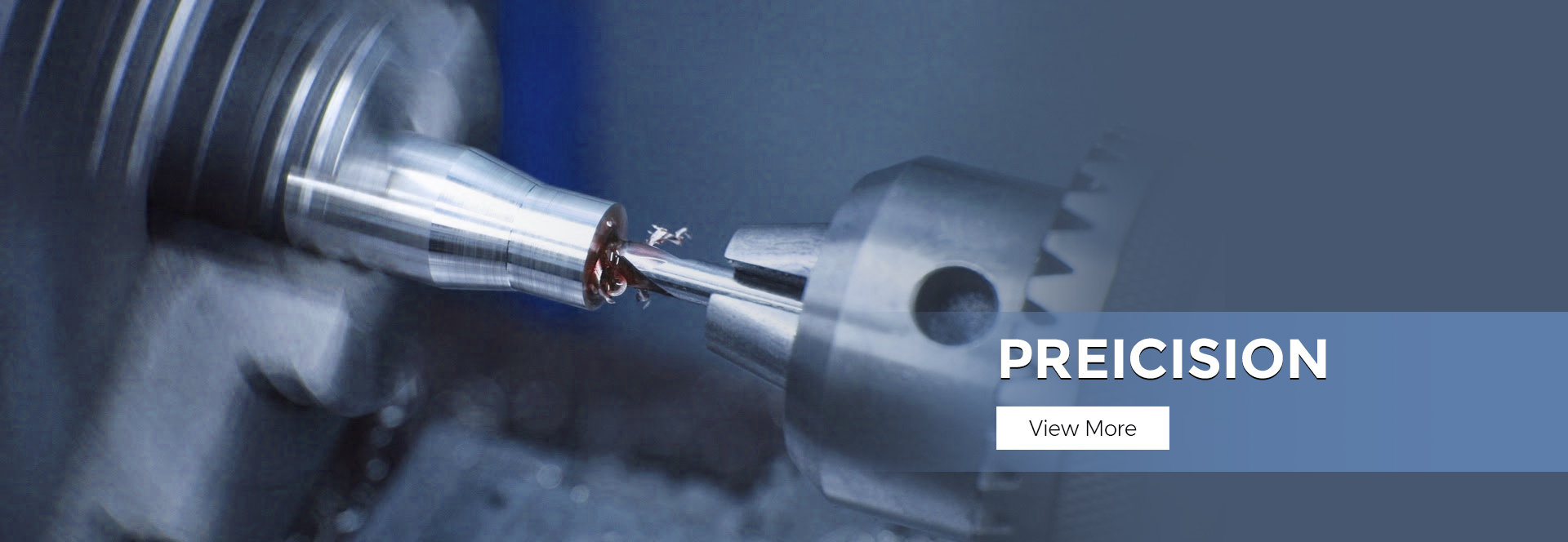
Additionally, the alloy's resistance to fatigue means that components cast from aluminium bronze can withstand repetitive stress cycles without cracking or failing Additionally, the alloy's resistance to fatigue means that components cast from aluminium bronze can withstand repetitive stress cycles without cracking or failing
aluminium bronze casting.
Artisans and engineers alike appreciate the workability of aluminium bronze. Despite its high strength, the alloy can be cast into complex shapes and machined to precise tolerances. This versatility allows designers to create intricate components that optimize performance and space utilization in tight quarters, such as engine blocks or pump systems.
However, the process of casting aluminium bronze requires expertise due to the alloy's tendency to form shrinkage voids during cooling. Master foundrymen employ techniques like risering and gating to compensate for this behavior, ensuring that the finished product is free from defects. Proper melt management and strict control over impurities further guarantee the quality and consistency of the cast parts.
In conclusion, aluminium bronze casting represents a pinnacle of achievement in the field of metallurgy. Its unique blend of properties – strength, toughness, wear resistance, and corrosion resistance – make it an indispensable material in industries ranging from marine to heavy machinery. As technology continues to evolve, the processes involved in casting aluminium bronze will likely become even more refined, pushing the boundaries of what is possible in industrial applications.