The Evolution of Turbo Housing Design A Journey of Innovation and Efficiency
In the realm of automotive engineering, the turbocharger has emerged as a revolutionary force, enhancing engine performance and efficiency while reducing emissions. One critical component in this sophisticated system is the turbo housing, which plays a pivotal role in the turbo's ability to harness and deliver exhaust gas energy. Over the years, the design of the turbo housing has undergone significant transformations, reflecting the relentless pursuit of improved performance and durability.
The early iterations of turbochargers featured relatively simple housing designs, often consisting of a cylindrical or conical shape with inlet and outlet ports. These early designs were adequate for their time, but they were limited by their inability to efficiently manage the high temperatures and pressures generated within the turbocharger. As a result, these early turbochargers were prone to premature failure and reduced efficiency.
In response to these challenges, engineers began exploring more advanced housing designs that could better withstand the rigors of high-performance applications. One such innovation was the adoption of a V-band clamp system, which provided a more secure and reliable seal between the housing and the turbine wheel. This innovation not only improved efficiency but also extended the life of the turbocharger by reducing the risk of leaks and failures.
Further advancements in materials science have also played a crucial role in the evolution of turbo housing design
Further advancements in materials science have also played a crucial role in the evolution of turbo housing design
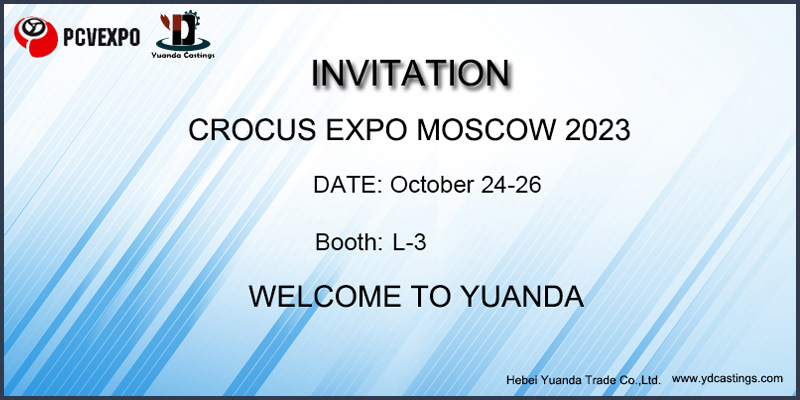
Further advancements in materials science have also played a crucial role in the evolution of turbo housing design
Further advancements in materials science have also played a crucial role in the evolution of turbo housing design
7.3 turbo housing. Today, many turbochargers utilize high-strength, lightweight materials such as titanium and aluminum alloys, which provide superior strength and corrosion resistance while reducing overall weight. These materials allow for more compact and efficient turbochargers, further improving engine performance and fuel economy.
Perhaps the most significant advancement in turbo housing design in recent years has been the introduction of variable geometry turbines (VGTs). These turbines feature adjustable vanes that can be adjusted in real-time to optimize gas flow based on engine demand. By varying the size of the inlet passage, VGTs are able to maintain optimal turbine speed over a wider range of engine operating conditions, resulting in improved power output and efficiency.
In conclusion, the evolution of turbo housing design has been a testament to the ingenuity and creativity of automotive engineers. From simple beginnings to the sophisticated designs of today, each iteration has brought us closer to realizing the full potential of turbocharged engines. As technology continues to advance, we can expect to see even more innovative designs and materials that will further enhance the performance and efficiency of these vital components.