Stainless Steel Casting Foundry A Comprehensive Guide
Stainless steel casting foundries play a crucial role in the manufacturing industry by producing high-quality stainless steel castings for various applications. These foundries utilize advanced technology and expertise to create components that meet the highest standards of quality, durability, and performance. In this article, we will explore the basics of stainless steel casting foundries, including their processes, materials, and applications.
Process Overview
The stainless steel casting process involves several steps, starting with the preparation of molten stainless steel. This molten metal is then poured into molds, which are designed to produce the desired shape and size of the casting. The mold is typically made of refractory materials, such as silica sand or ceramic, which can withstand the high temperatures involved in the casting process.
Once the molten steel has been poured into the mold, it is allowed to cool and solidify. This process can take anywhere from a few hours to several days, depending on the size and complexity of the casting. After the steel has solidified, the mold is broken open to reveal the finished casting.
Materials Used
Stainless steel casting foundries use a variety of materials to produce their castings, including stainless steel alloys, pig iron, and other metals. Stainless steel alloys are popular choices due to their excellent corrosion resistance, high strength, and good weldability. Some common types of stainless steel used in casting include 304, 316, and 430.
Pig iron is also used in some casting processes, particularly those that require higher melting temperatures
Pig iron is also used in some casting processes, particularly those that require higher melting temperatures
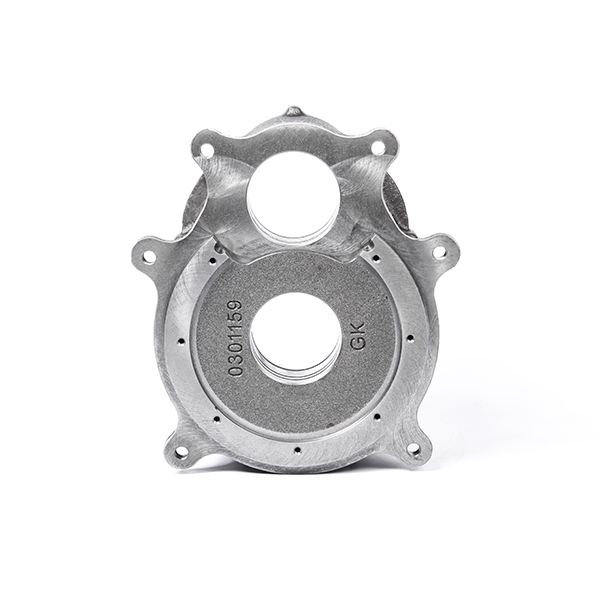
Pig iron is also used in some casting processes, particularly those that require higher melting temperatures
Pig iron is also used in some casting processes, particularly those that require higher melting temperatures
stainless steel casting foundry. Other metals, such as aluminum and copper, may be used in specific applications where their unique properties are required.
Applications
Stainless steel castings are used in a wide range of industries, including automotive, aerospace, construction, and chemical processing. They are particularly well-suited for applications where high strength, corrosion resistance, and good appearance are critical.
In the automotive industry, stainless steel castings are used to produce engine blocks, transmission cases, and exhaust manifolds. Aerospace applications include fuel tanks, engine components, and landing gear parts. Construction uses include pipes, fittings, and valves for water and gas distribution systems. Chemical processing facilities rely on stainless steel castings for reactors, vessels, and piping systems.
Conclusion
Stainless steel casting foundries are essential to modern manufacturing, providing high-quality castings for a wide range of applications. By utilizing advanced technology and expertise, these foundries can produce components that meet the highest standards of quality, durability, and performance. As the demand for stainless steel products continues to grow, the role of stainless steel casting foundries will only become more important.