The Significance of 1 4 Pipe Cap A Vital Component in Industrial Pipelines
In the world of industrial engineering, play an indispensable role in ensuring the efficient and safe flow of materials. Among these accessories, the 1 4 pipe cap stands out as a critical component, providing both functionality and reliability. This seemingly small part is instrumental in numerous applications, ranging from oil and gas pipelines to chemical processing plants.
A pipe cap, often referred to by its dimension code 1 4%, is a type of end closure designed to seal the end of a pipe. The '1' signifies the nominal pipe size, which typically refers to the approximate inner diameter of the pipe, while '4' indicates the schedule or wall thickness. This specific size is commonly used in medium to high-pressure systems where robustness and durability are paramount.
The primary function of a 1 4 pipe cap is to prevent leakage and protect the internal contents of the pipe from external elements such as dust, moisture, or debris. It serves as a barrier, ensuring that the pipeline remains sealed and secure during non-operative periods or when the pipe's end needs to be temporarily closed.
In industries like petrochemicals, where hazardous substances are transported, the importance of a reliable pipe cap cannot be overstated. It prevents accidental spills, reducing environmental risks and potential safety hazards for workers It prevents accidental spills, reducing environmental risks and potential safety hazards for workers
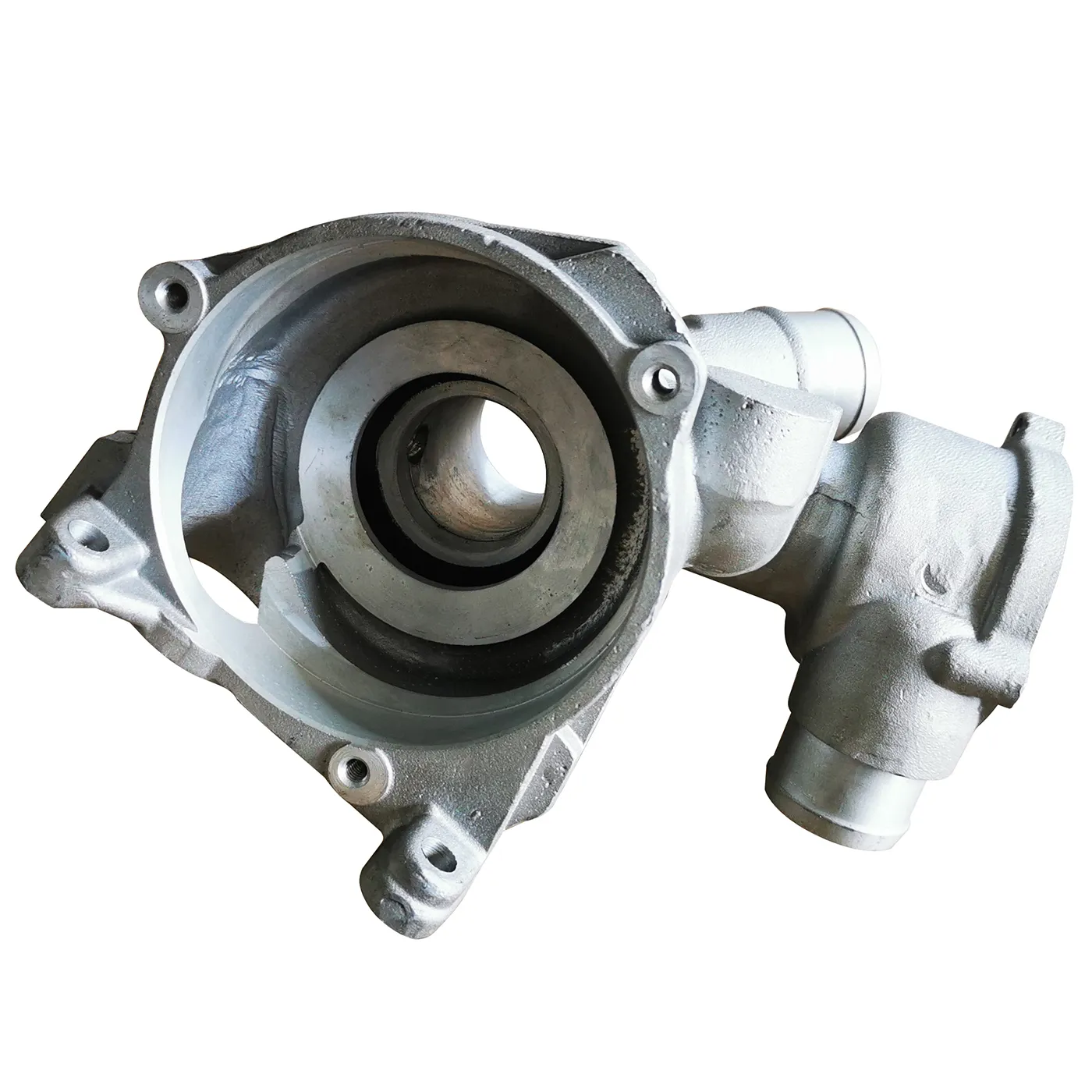
It prevents accidental spills, reducing environmental risks and potential safety hazards for workers It prevents accidental spills, reducing environmental risks and potential safety hazards for workers
1 4 pipe cap. In addition, the use of 1 4 pipe caps in construction projects helps maintain structural integrity by safeguarding open pipe ends from damage during transportation, storage, or installation.
Moreover, pipe caps also find application in pressure testing, where they are temporarily installed to create a environment for conducting tests. They are made from materials like carbon steel, stainless steel, or alloy steel, ensuring resistance to corrosion and high-temperature conditions, thereby enhancing their longevity and performance.
Manufacturing standards like ANSI (American National Standards Institute) and ASME (American Society of Mechanical Engineers) dictate the design and quality of 1 4 pipe caps, ensuring they meet stringent safety and performance requirements. These standards guarantee that the pipe caps can withstand the pressures and conditions they will encounter in their respective industries.
In conclusion, the 1 4 pipe cap, despite its modest appearance, plays a significant role in the complex and demanding world of industrial piping. Its importance lies not only in its ability to seal and protect but also in its adherence to safety norms and its contribution to overall system integrity. As technology advances and industries evolve, the significance of this humble component will continue to resonate, ensuring smooth and secure operations across various sectors.