Casing in centrifugal pumps is an integral component that often doesn’t get the attention it deserves. This crucial element not only houses the impeller but also plays a significant role in dictating the performance, efficiency, and lifecycle of the pump. Understanding the intricacies of pump casing can profoundly impact the selection process and operation of centrifugal pumps in various industrial applications.
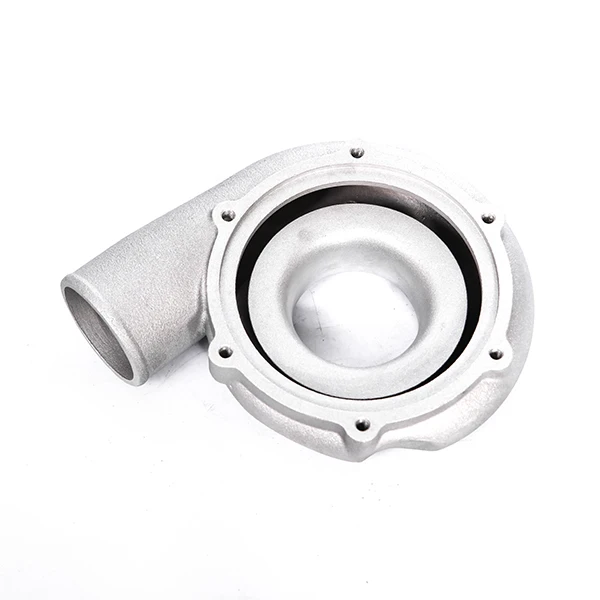
One of the primary functions of the casing is to convert the velocity of the fluid coming from the impeller into a controlled flow, usually characterized by increased pressure. This transformation is vital for the pump’s efficiency and can be influenced by the design of the casing. A well-designed casing ensures minimal hydraulic loss, thereby enhancing the overall efficiency of the pump. For optimal performance, selection of the casing must match the specific requirements of the application, such as fluid type, pressure, and flow rate.
In centrifugal pumps, two predominant types of casings exist volute and diffuser. The volute casing is one of the most common types, designed to decrease the speed of the fluid and convert kinetic energy into pressure energy. Made with a spiral structure that increases in area as it approaches the discharge port, a volute casing serves to evenly distribute pressure and reduce radial loads on the shaft, thus prolonging the lifespan of the pump. While advantageous in many applications, volute casings might not achieve optimal efficiency with heads less than 150 ft and might be subject to imbalanced pressure along different directions.
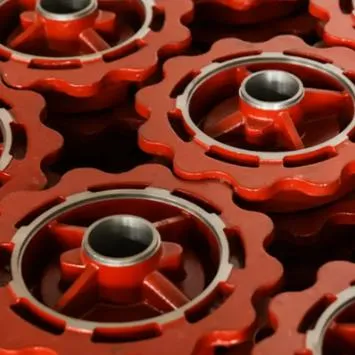
The diffuser casing, on the other hand, employs a series of stationary vanes surrounding the impeller. These vanes aid in slowing down the fluid and converting kinetic energy into pressure more efficiently than volute designs in certain scenarios. Diffuser casings tend to offer enhanced control over the flow profile and pressure distribution, conserving energy while maintaining higher efficiency across diverse operating conditions. Industries requiring high efficiency and reliability, such as petrochemical and water supply operations, often favor pumps with diffuser casings.
casing in centrifugal pump
Material selection for pump casing is another critical factor affecting reliability and longevity. Casing materials need to withstand the chemical properties of the pumped fluid, operating temperatures, and pressure situations. Common materials include cast iron, ductile iron, stainless steel, and various polymers, each suitable for different applications. For instance, stainless steel offers excellent corrosion resistance, making it ideal for pumping aggressive chemicals, whereas polymers might be utilized in less demanding water applications due to their cost-effectiveness and corrosion resistance.
Regular maintenance and inspection of pump casings is necessary to prevent leaks, erosions, and other potential failures. Maintenance experience shows that neglecting the condition of the casing can lead to increased wear and energy consumption, and eventually, unplanned downtimes, profoundly impacting operations and costs. Engaging in routine checks can avert potential issues, ensuring that the pump runs smoothly over its designated lifespan. Experienced engineers also advise monitoring vibration and noise levels, as abnormal values could indicate issues with not only the casing but the pump’s overall operation.
Centrifugal pump casing, though often overlooked, represents a core component that requires careful consideration and expertise during selection and operation. By addressing the nuances in casing design, material selection, and maintenance, industries can not only optimize pump performance but also ensure long-term reliability and cost-efficiency. When well-informed decisions are made regarding pump casing, the whole pump system is better positioned for success, translating to improved operational uptime and energy, and ultimately advancing the entirety of fluid management processes.