Rotating impellers play a crucial role in various industrial and consumer applications, ranging from water pumps to complex HVAC systems. The innovation behind rotating impeller designs stands as a testament to engineering expertise and precision crafting, ensuring efficiency and reliability across diverse industries. As such, it is essential for businesses to understand the nuances of this technology to achieve optimal functionality and cost-effectiveness in their operations.
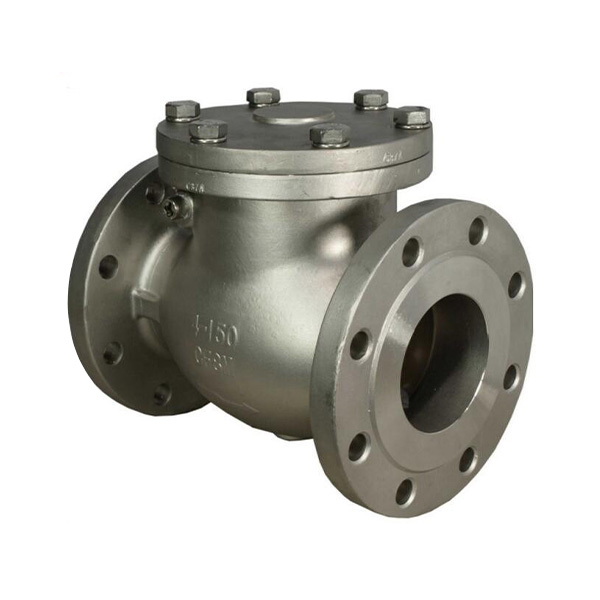
One key aspect of rotating impellers is their ability to improve system efficiency through fluid dynamics. By understanding the flow of liquids or gases through impeller blades, engineers can optimize designs to reduce turbulence and energy consumption. Each rotation of the impeller displaces fluid in a manner that maximizes output while minimizing input power requirements. Therefore, businesses looking to enhance their operational efficiency can significantly benefit from strategically selecting and deploying advanced impeller systems tailored to their specific needs.
Material selection is another critical component influencing impeller performance and longevity. Typically constructed from durable materials like stainless steel, titanium, or specific polymers, impellers are designed to withstand harsh environmental conditions and resist wear. The choice of material depends heavily on the application—chemically resistant compounds are preferable in industries handling corrosive substances, while lightweight alloys may be prioritized in aerospace applications to reduce overall weight.
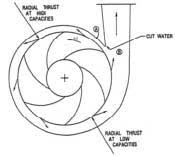
Expertise in fluid mechanics and materials science is pivotal for companies seeking to leverage the full potential of rotating impellers. Specialists within these fields can provide invaluable insights into customization options, helping to craft impellers that meet unique operational demands. Businesses can gain competitive advantages by collaborating with professionals who understand the intricacies of impeller mechanics and material properties, ensuring that their systems not only meet but exceed performance expectations.
rotating impeller
Trustworthiness and authoritativeness in the production and modification of rotating impeller systems are built on rigorous testing and quality control. Manufacturers employing state-of-the-art testing protocols ensure that each impeller meets stringent structural and operational standards. Companies should seek partnerships with manufacturers who demonstrate a commitment to excellence through certification and adherence to international quality standards, thus securing reliable performance metrics and reducing the risk of system failures.
Furthermore, the installation and maintenance of impeller systems require skilled personnel to ensure longevity and performance sustainability. Improper handling or installation can compromise system integrity, leading to inefficiencies and potential breakdowns. Regular maintenance, including inspection for wear and tear and the timely replacement of worn components, is essential to extend the lifespan of impeller systems. Engaging with experienced service professionals for these tasks can cultivate confidence in system reliability and operational stability.
The future of rotating impeller technology is poised for transformative advancements, integrating smart technologies and sensor capabilities to further enhance functionality. The rise of IoT (Internet of Things) in industrial applications is fostering impeller designs that can self-monitor, communicate performance parameters, and predict maintenance needs before issues arise. This trend towards predictive maintenance and real-time analytics is set to revolutionize industries dependent on fluid control systems, pushing the envelope of what is possible with rotating impeller technology.
For businesses aiming to stay ahead in competitive markets, embracing the latest advancements in rotating impeller design and functionality is imperative. By combining industry-leading expertise, cutting-edge materials, and robust maintenance practices, companies can harness the full spectrum of benefits that modern impeller systems offer. Ultimately, the strategic implementation of rotating impeller technology not only enhances operational efficiency but also underscores a commitment to innovation and excellence in practice.