In the realm of industrial mixing, the role of the mixing impeller is critically pivotal, exemplifying the convergence of meticulous engineering and applied physics. These indispensable components drive the efficacy of blending processes across diverse industries, from pharmaceuticals to wastewater treatment. The artistry in impeller design lies not only in its configuration but also in its application-specific precision.

Central to the evolution of mixing impeller technology is the understanding of fluid dynamics and the nature of the materials being mixed. This understanding translates into design choices that optimize performance metrics such as mixing efficiency, shear rates, and power consumption. The choice of the impeller significantly influences the homogeneity and stability of the mixture, paving the way for innovation and increased productivity.
Current industry trends showcase a growing inclination towards tailored impeller designs, calibrated for specific applications. This movement is driven by the necessity for materials compatibility, precision in viscosity management, and compliance with regulatory standards. Consequently, the fabrication of impellers now involves a symbiotic process between computational fluid dynamics (CFD) modeling and empirical testing, ensuring robustness in diverse operational settings.
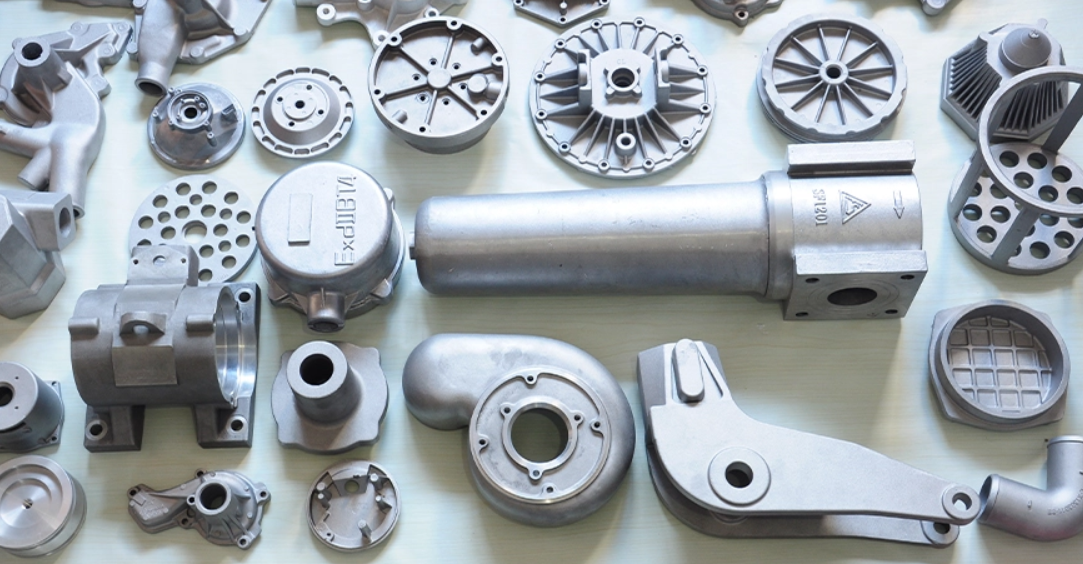
A vital consideration in impeller selection is the design configuration, including axial flow, radial flow, and mixed flow patterns. Axial flow impellers, such as marine propellers, are celebrated for their ability to induce bottom-to-top mixing, ensuring thorough material integration. Conversely, radial flow impellers, exemplified by Rushton turbines, are adept at shear-intensive tasks, ideal for emulsification processes. Mixed flow impellers, like hydrofoils, offer the benefits of both axial and radial types, providing versatile solutions across multifaceted mixing scenarios.
Materials of construction play a critical role in impeller performance, with options ranging from stainless steel to high-performance alloys and composites. The choice is governed by considerations such as corrosion resistance, structural integrity under stress, and inertness to reactive substances. For products that demand stringent hygiene standards, such as in the food and pharmaceutical sectors, smooth, polished finishes are indispensable to prevent contamination and facilitate cleaning.
mixing impeller
The interdependence between impellers and their operating environments can be elaborated through a case study from the biopharmaceutical industry. In bioreactor systems,
impeller design is crucial for maintaining viable cell cultures. The shear-sensitive nature of biological cells demands impellers that promote gentle mixing to prevent cell lysis. Here, well-designed Scaba impellers or marine-type impellers are leveraged to achieve the delicate balance of efficient gas dispersion while preserving cell integrity.
Expert consultation plays a significant role in navigating the complexities of mixing impeller selection. Professionals equip engineers with the know-how to match process necessities with impeller capabilities, considering variables like tank geometry, fluid viscosity, and scale of operation. The schematic setup of the mixing vessel and the anticipated reaction kinetics further influence impeller design decisions, making expertise an invaluable asset in the process.
The authoritative knowledge of impeller dynamics extends beyond enhancing operational efficiencies; it encompasses compliance with environmental and safety standards. Trustworthiness in performance and predictability is non-negotiable, necessitating rigorous testing and validation procedures. Manufacturers are thus bound to standardized practices, ensuring that their impellers meet the highest benchmarks of reliability and safety across varied application domains.
In the quest for enhanced mixing performance, innovations such as hybrid impellers, adjustable pitch systems, and impellers with surface modifications are emerging. These advancements promise not only to meet existing challenges but also to anticipate future demands for energy-efficient and cost-effective mixing solutions.
The ongoing exploration and implementation of state-of-the-art impeller designs underscore the intersection of tradition and technology. As industries evolve, the role of the mixing impeller remains a testament to the unyielding commitment to advancing efficiency and excellence in industrial processes.