CF8 and CF8M are two distinct grades of stainless steel used primarily in the manufacturing of valves, pumps, and various industrial components. Their composition provides them with specific properties ideal for certain applications, yet they are often misunderstood or used interchangeably with inadequate regard for their unique characteristics. Understanding CF8 and CF8M requires diving deep into their metallurgical content, characteristics, and suitability for different industrial applications.
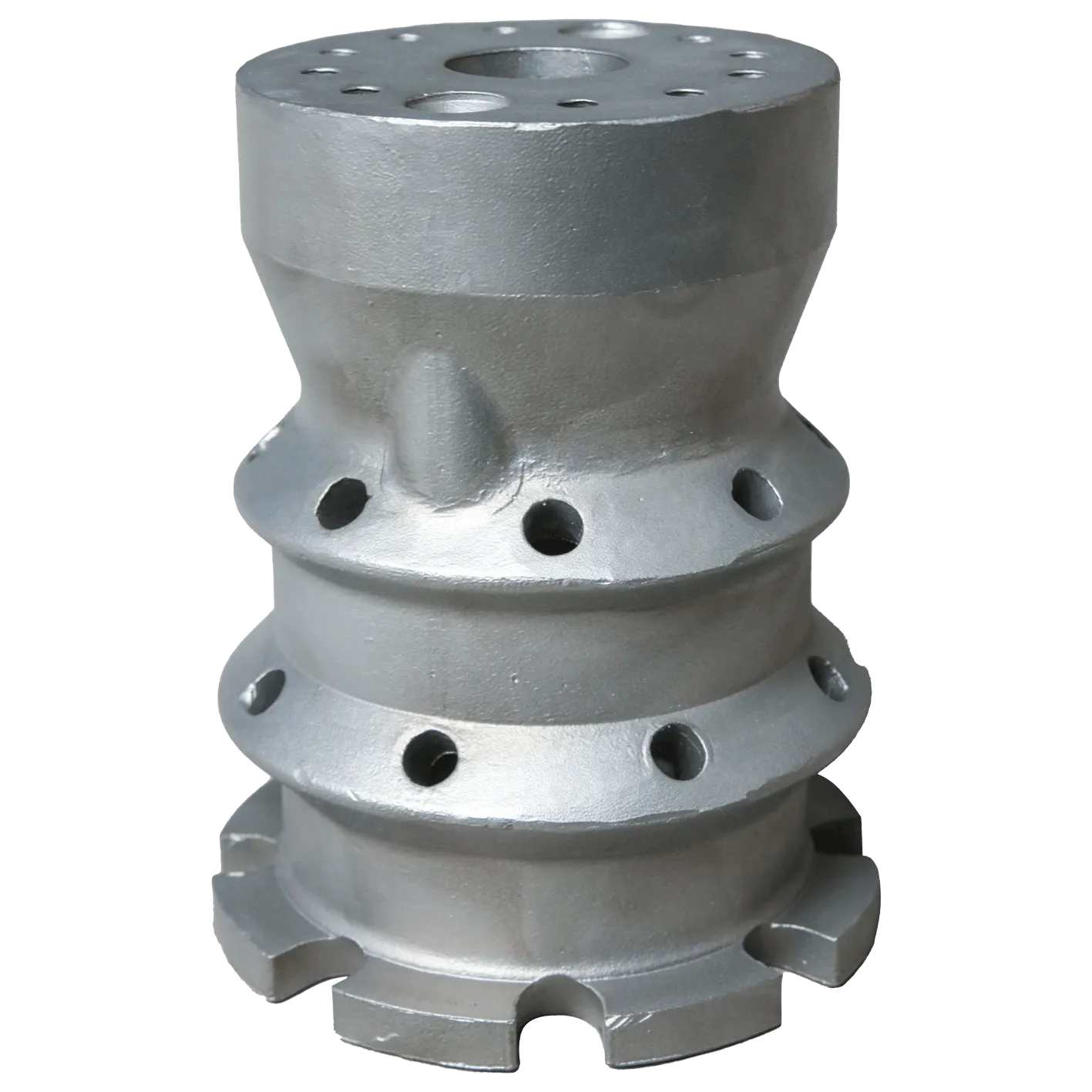
CF8 is a cast austenitic steel grade equivalent to the wrought 304 stainless steel. It contains approximately 18% chromium and 8% nickel, which gives it impressive corrosion resistance and strength. CF8 is particularly well-suited for environments where both corrosion and strength are critical. It performs admirably in maritime environments, food processing, and architectural applications due to its ability to withstand chemical exposure and environmental wear. However, CF8 might not be suitable for all chemical environments, especially those with high chloride content, as it can be susceptible to pitting and crevice corrosion.
CF8M, on the other hand, is an advancement of CF8 with the addition of molybdenum. This additional element significantly enhances its corrosion resistance, especially against chlorides and other aggressive agents that commonly cause deterioration in stainless steel. CF8M is, therefore, an ideal choice for harsh environments found in chemical processing, offshore oil drilling, and even medical apparatus. Its robustness against pitting makes it indispensable in processes involving salt water or acids.
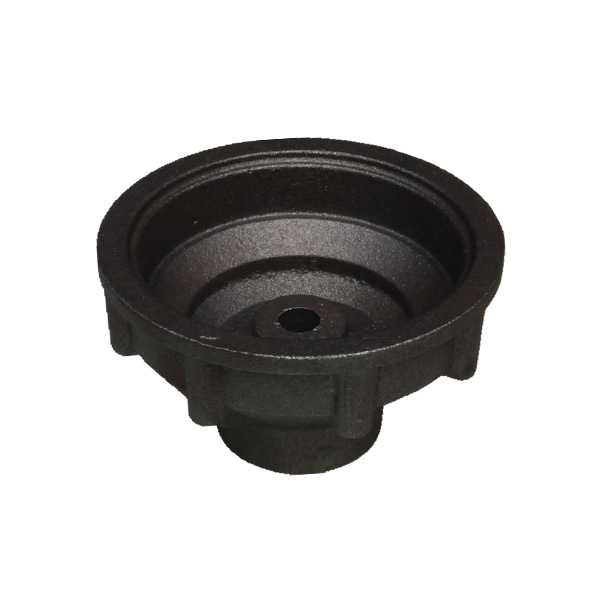
Both CF8 and CF8M share several mechanical properties, such as high tensile strength and toughness, which make them favored materials for components that must endure mechanical stress. Both steel grades are resistant to oxidation at elevated temperatures, although CF8M offers superior protection due to the presence of molybdenum. This quality is crucial in preventing degradation in high-temperature applications, making CF8M more reliable for results in processes like power generation or manufacturing of heat exchangers.
cf8 and cf8m
One of the core benefits of using CF8 and CF8M in manufacturing is their ease of casting and machining. These materials can be fabricated into complex shapes without losing their structural integrity. Their adaptability to welding processes also means they can be integrated into larger assemblies without compromising the joints' corrosion resistance — a critical factor in ensuring component longevity in corrosive environments. Notably, the ease of machinability of CF8 and CF8M translates into reduced production costs, as less processing time is needed to produce complex components.
While both CF8 and CF8M have their exclusive advantages, the choice between them hinges on the specific environmental conditions and mechanical requirements of the application. CF8 could be more cost-effective for environments with moderate corrosive elements, while CF8M, although slightly more expensive, offers peace of mind and reliability in harsh, chemically aggressive environments. Engineers and material specialists must carefully consider the application's unique requirements, often performing thorough analysis and testing to identify which alloy will yield the most efficient and effective results.
Importantly, the selection of CF8 or CF8M should be aligned with regulatory standards and certifications pertinent to industry applications. Adherence to standards such as ASTM A351/A351M or ASTM A744/A744M can provide assurance of the material's quality and performance capabilities. Moreover, third-party validation and supplier credentials should be considered to ensure the authenticity and reliability of the stainless steel being utilized.
In summary, CF8 and CF8M stainless steels are distinguished not only by their chemical compositions but also by the specific applications for which they are best suited. Their distinct properties make them versatile and reliable choices for manufacturers seeking materials that offer both strength and corrosion resistance. The decision to use CF8 or CF8M should be guided by a thorough understanding of the environmental conditions, stress factors, and regulatory requirements. Such attention to detail will ensure that the stainless steel selected not only meets but exceeds the operational performance expectations, thus reinforcing its role as an indispensable component in varied industrial applications.