The aluminium impeller stands at the forefront of modern engineering, representing a critical component in various industrial and commercial applications, from automotive to aerospace. Engineered for excellence, aluminium impellers combine lightweight properties with outstanding strength, corrosion resistance, and thermal conductivity. These characteristics make them a preferred choice across industries aiming for efficiency and reliability.
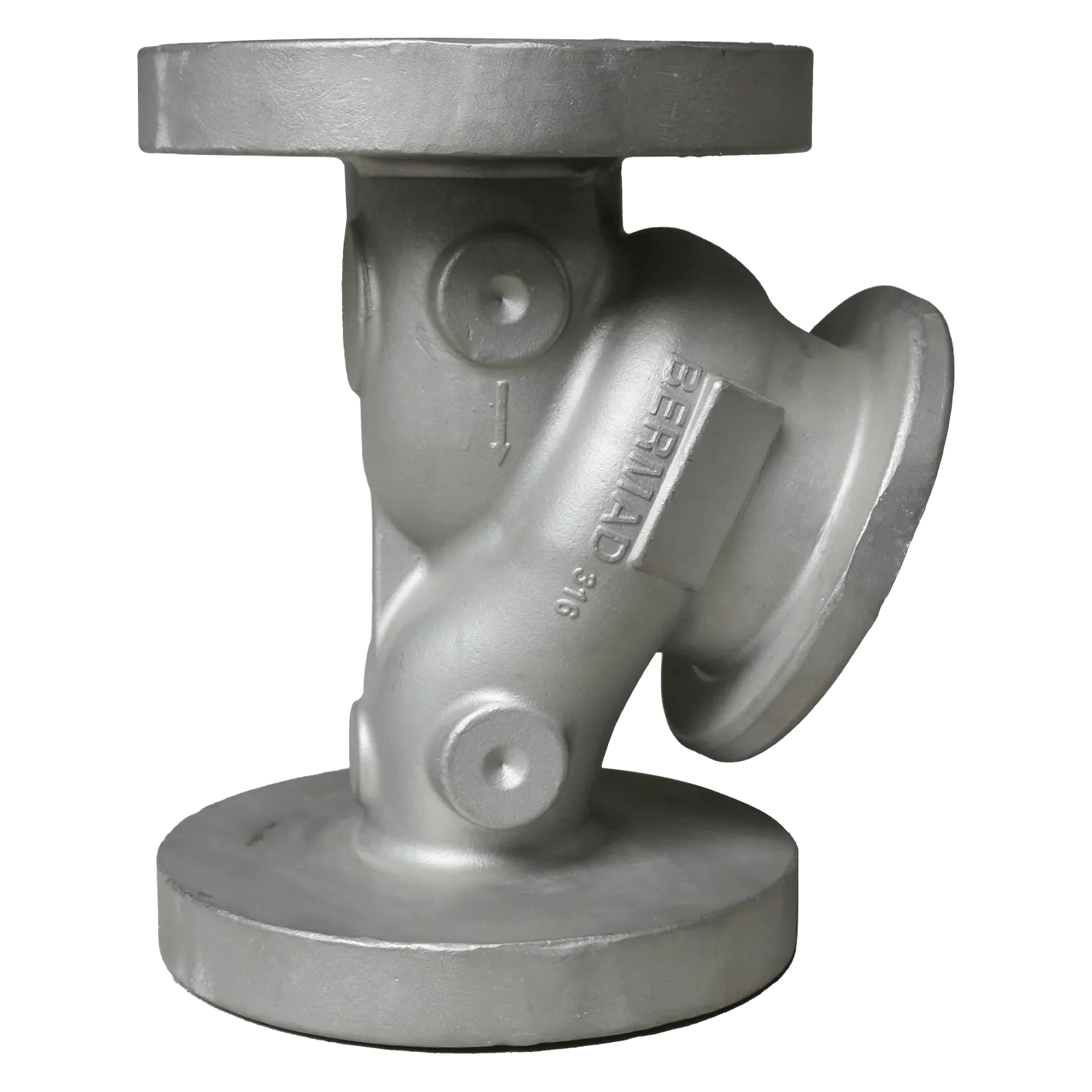
Aluminium, known for its strength-to-weight ratio, offers a perfect balance for impellers that demand both durability and nimbleness. Unlike traditional materials, aluminium reduces the overall weight of machinery, which in turn enhances fuel efficiency and reduces emissions. Vehicles equipped with aluminium impellers, for example, benefit from improved performance and longevity, aligning with sustainable practices by lowering carbon footprints.
The production of aluminium impellers involves advanced metallurgy techniques. Aluminium alloys, particularly those with magnesium and silicon, are crafted to enhance mechanical properties. The casting or machining process is meticulously controlled, ensuring precision and uniformity, which are critical for impellers' balanced rotation and optimal performance. Technological advancements in computer-aided design (CAD) and computational fluid dynamics (CFD) further enhance the precision of aluminium impeller manufacturing. These technologies simulate various operational conditions, allowing for the optimization of design and efficiency before physical production begins.
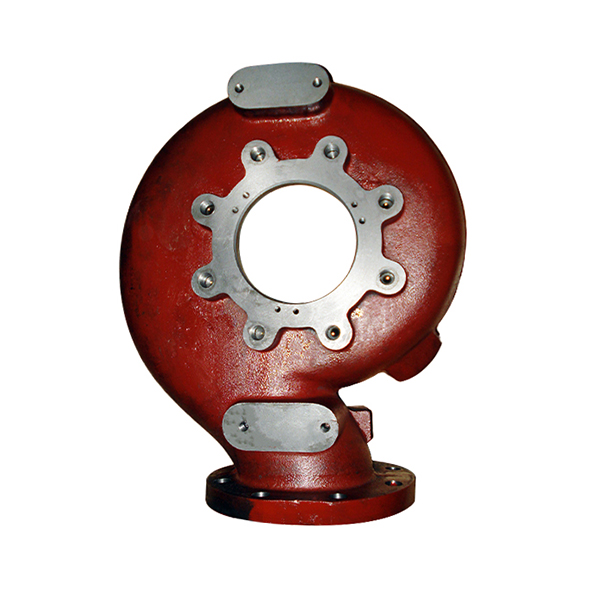
Professional expertise in the field reveals that one of the unique advantages of aluminium impellers is their adaptability to custom specifications. Industries such as HVAC (heating, ventilation, and air conditioning) and marine propulsion depend significantly on bespoke solutions due to varying demands in size, shape, and operational environment. Aluminium’s malleability makes it easier for manufacturers to tailor impellers to specific needs without compromising structural integrity or performance.
aluminium impeller
Moreover, the authoritative use of aluminium impellers in turbomachinery showcases their critical role in enhancing pressure and flow in systems like compressors and pumps. Their capability to withstand high-temperature environments without losing efficacy is a testament to their robustness. This exceptional performance is backed by rigorous industry standards and certifications, further establishing trustworthiness in their application.
In an era where technology and connectivity define operational success, the integration of smart systems within aluminium impellers marks a new frontier. Sensors embedded within these impellers can provide real-time data on performance metrics such as temperature fluctuations, pressure levels, and rotational speed. This data-driven approach not only optimizes performance but also preemptively addresses maintenance needs, preventing costly downtimes.
For industries prioritizing efficiency and sustainability, the recycling aspect of aluminium impellers cannot be overstated.
Aluminium is infinitely recyclable, maintaining its properties without degradation. This aspect not only contributes to environmental conservation but also reduces raw material costs, offering economic benefits to businesses aiming for sustainable practices.
In summary, the aluminium impeller is more than just a mechanical component; it encapsulates the ideals of modern engineering—efficiency, precision, and sustainability. Through continuous innovation and adherence to the highest standards, aluminium impellers are set to revolutionize industry practices, offering unparalleled reliability and performance. Businesses investing in aluminium impellers are not merely enhancing their operational capacities but are also committing to a future of sustainable and advanced engineering solutions.