Impellers are critical components in the engineering world, playing an integral role in various applications ranging from industrial machinery to everyday household appliances. Understanding the different types of impellers helps in maximizing efficiency, performance, and longevity of machines involved in fluid dynamics. The expertise behind the design and application of these devices is both an art and a science, requiring a blend of engineering knowledge and practical experience.
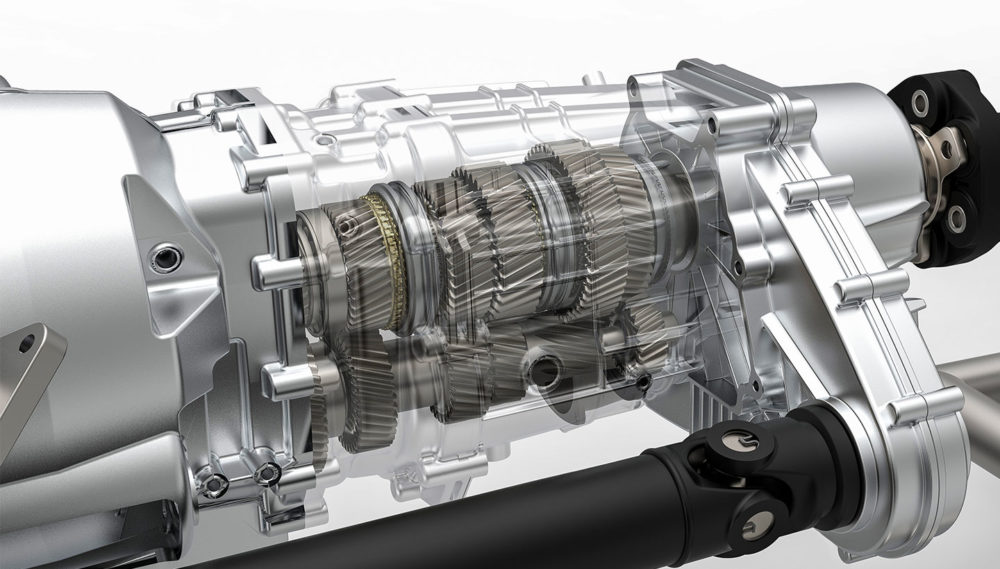
One of the most common types of impellers is the closed impeller. This design includes sidewall components that create a tight seal, reducing fluid slip and increasing efficiency. Closed impellers are frequently used in applications where there is a need for high head or high-pressure operations, such as water supply systems or chemical processing. Their enclosed design minimizes leakage, which is crucial in maintaining a controlled environment, enhancing trustworthiness for industries reliant on precise fluid management.
On the other hand, open impellers feature vanes that stand free, typically attached to a central hub without sidewall enclosure. These impellers are easier to clean and maintain, making them ideal in applications where clogging is a concern, such as in handling wastewater or slurries. Their simplicity doesn’t just offer easy maintenance but also reliability; they tolerate larger clearances, reducing the risk of damage from particles within the fluid.
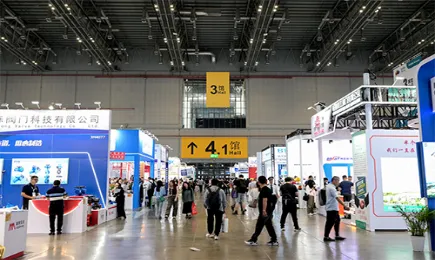
Semi-open impellers present a hybrid between closed and open designs, featuring a back plate for stability while leaving the vanes exposed on one side. This design offers a balance of efficiency and ease of maintenance. Semi-open impellers are often used in situations requiring moderate handling of solids, such as in some agricultural and food processing applications. Their versatility ensures satisfactory performance across a wide range of conditions, showcasing expert adaptability in fluid handling operations.
In axial flow impellers, fluid moves parallel to the impeller shaft, making them suitable for low head and high flow applications. These impellers are commonly found in ventilation systems, cooling towers, and some types of pumps. The efficient design facilitates excellent flow rates with minimal energy consumption, representing a masterful application of aerodynamic principles in mechanical engineering.
different types of impellers
Radial flow impellers, by contrast, move fluid perpendicular to the shaft. This design is synonymous with high pressure and low flow applications, excelling in centrifugal pumps used for high-pressure fluid transportation. The robust nature of radial flow impellers underscores their reliability and authority in systems that depend on consistent, high-pressure delivery.
Mixed flow impellers incorporate elements from both axial and radial designs, offering a compromise between high flow and high head, thus catering to a wide array of industrial processes. They are often utilized in situations that demand efficient transfer of fluids over considerable distances without excessive pressure loss, aligning with the premium standards of modern engineering solutions.
The materials used in constructing impellers also speak to the expertise and authoritative knowledge employed in their design. Stainless steel, bronze, plastic, and composite materials are selected based on the working environment, including the fluid’s chemical composition, temperature, and pressure. Each material confers specific benefits, from corrosion resistance to cost-effectiveness or lighter weight, contributing to the overall efficiency and durability of the machinery involved.
Whether it's in the selection of an impeller for a new pump design or the replacement in an existing system, understanding the differences and applications allows engineers to make well-informed decisions. Experience drives the industry forward, with continuous improvements in impeller design based on field performance and evolving technological innovations. Trust in the engineering behind impellers stems from their proven capabilities in diverse settings, ensuring that they continue to be indispensable components across industrial sectors.