Centrifugal pump volute casing plays a pivotal role in optimizing the efficiency and reliability of centrifugal pumps across various industrial applications. With years of experience working with a myriad of pump systems, it is clear that the design and functionality of the volute casing can dramatically influence the performance metrics such as flow rate, efficiency, and longevity of the pump itself.
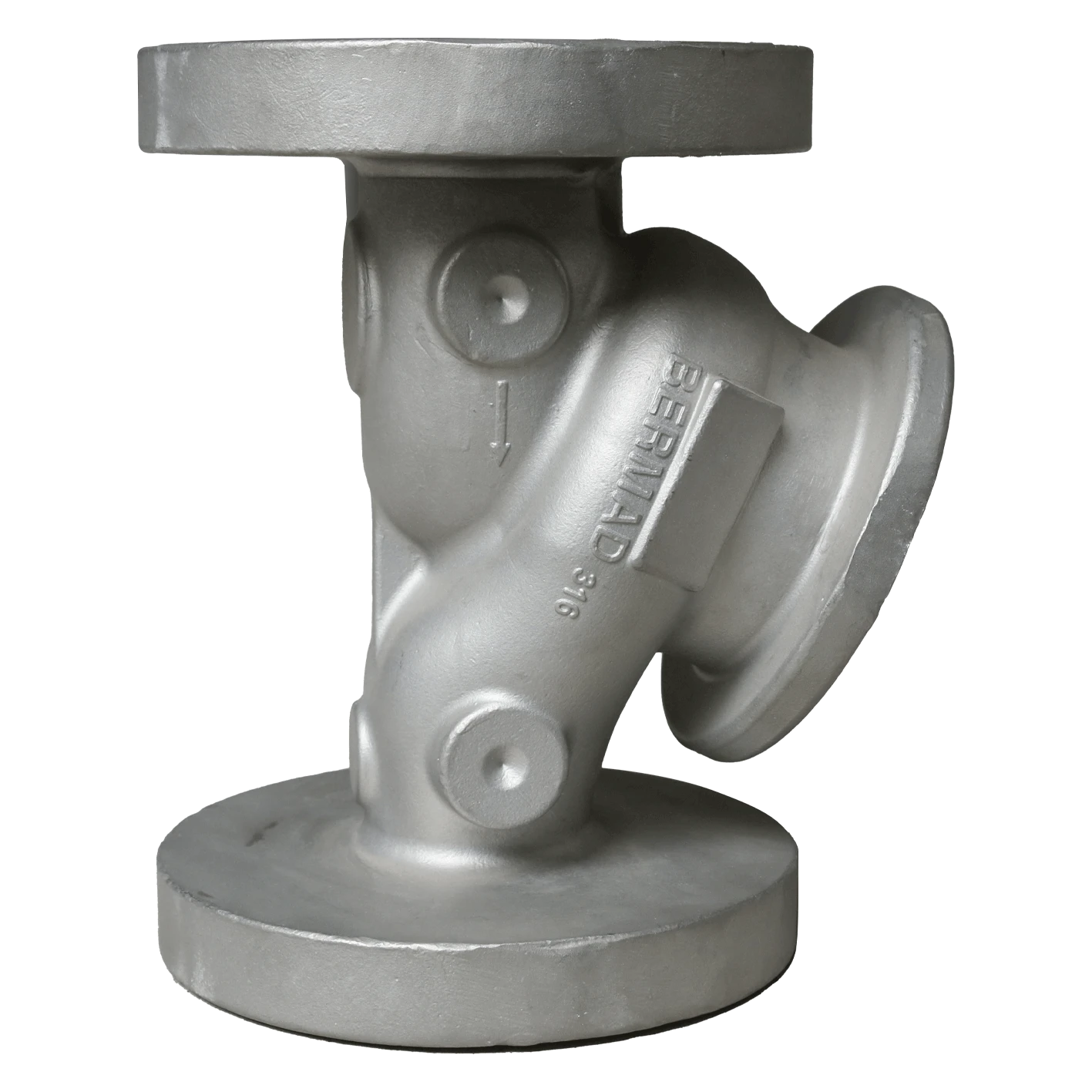
Understanding the unique engineering behind the volute casing is essential for both seasoned professionals in fluid dynamics and businesses looking to enhance their operational efficiency. The volute casing serves to convert the kinetic energy imparted to the fluid by the pump impeller into pressure energy as the fluid exits the pump. This transition is facilitated by the casing’s spiral shape which allows for the controlled expansion of fluid flow, thereby reducing velocity and increasing pressure.
From an engineering perspective, the design intricacies of volute casings necessitate a thorough grasp of fluid mechanics. Optimal volute casing design requires precise calculation of the volute’s cutwater gap – the space between the impeller and the volute tongue – which is crucial for minimizing hydraulic losses and potential cavitation issues. Furthermore, variations in volute casing materials and configurations can significantly affect the robustness and suitability of the centrifugal pump for different types of fluids, including those that are abrasive or corrosive.
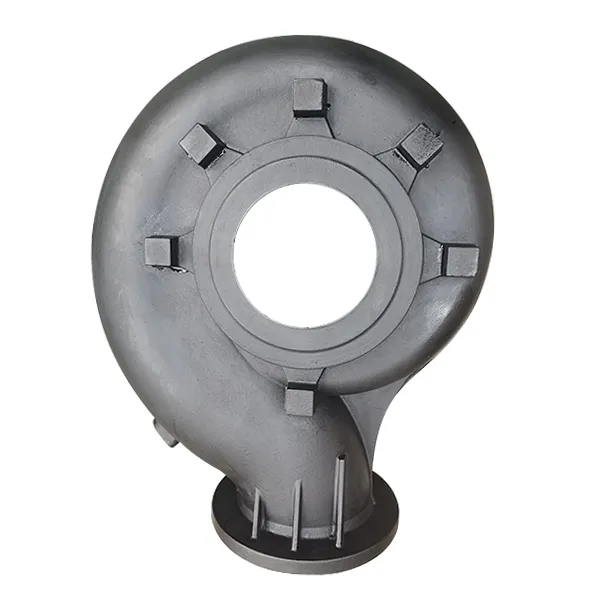
The expertise required to create an effective volute casing extends to understanding how different design alterations can enhance performance under particular operating conditions. For instance, double volute casings are particularly advantageous for applications requiring minimized radial load on the shaft, thereby reducing wear and extending the lifespan of the pump.
centrifugal pump volute casing
Industry experts often encounter the challenge of balancing production costs with performance gains. It’s important to consider the materials used; for instance, while cast iron may suffice for standard applications, stainless steel could be necessary for environments with stringent hygiene standards or exposure to corrosive substances.
Equally important is the authoritative insight provided by formal standards and guidelines issued by recognized entities such as the Hydraulic Institute. These set the benchmarks for manufacturing volute casings and ensure they adhere to industry standards, assuring end-users of their reliability and efficiency.
Establishing trust with clients or stakeholders regarding the effectiveness of a chosen volute casing design relies heavily on empirical performance data and case studies demonstrating real-world application successes. Companies with a history of proven excellence and patented technologies in centrifugal pump manufacturing further enhance their credibility by showcasing testimonials and quantifiable benefits realized by their clients.
In conclusion, centrifugal pump volute casings are more than just an assembly component; they are a critical element in achieving overall system efficiency and reliability. Mastery of the variables influencing volute casing performance not only demands a foundation of theoretical knowledge but also practical experience and adherence to industry standards, all of which collectively underpin a company’s reputation for providing trusted, authoritative solutions in centrifugal pump technology.