Understanding the complexities of industrial machinery is crucial for businesses seeking competitive advantage. One such significant element in these machines is the impeller wheel, a component whose design and function hold considerable merit in various sectors, including manufacturing, automotive, and aeration systems.
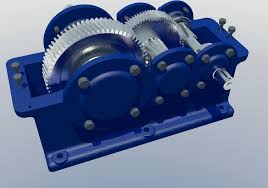
The impeller wheel is central to the functioning of pumps and turbines, operating as the driving force behind fluid movement. Featuring a series of specially designed blades, the impeller wheel harnesses rotational energy from a motor to move fluids efficiently. Its effectiveness is measured not just by its ability to move water, gas, or other substances but also by its stability under high pressure and its efficiency in conserving energy.
From a professional expertise standpoint, engineers give immense attention to the material composition and blade design of impeller wheels. The selection of materials often involves high-strength alloys that can withstand harsh environments, thereby enhancing durability and reducing wear and tear over time. The intricacy in blade design, whether backward-curved, forward-curved, or radial, significantly influences fluid dynamics and the overall efficiency of the machinery.
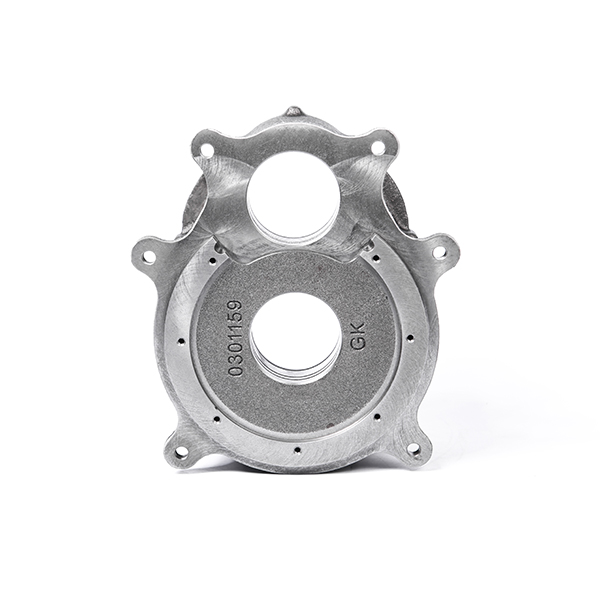
In industries such as oil and gas, where precision and reliability are paramount, the sophistication involved in crafting impeller wheels has evolved over the years. Advanced computational fluid dynamics (CFD) and finite element analysis (FEA) are employed to simulate and refine the efficiency of impeller designs before they even hit the production line.
Such modern approaches ensure not only enhanced performance but also adherence to regulatory standards.
Experience with impeller wheels also underscores the importance of maintenance and regular inspections. Even the most meticulously designed impeller wheel can suffer from issues such as cavitation or corrosion, which can severely impact system performance. Practical field knowledge highlights the necessity of routine maintenance schedules and the use of specific protective coatings which can prolong the life of the impeller wheel considerably.
impeller wheel
A noted authority in the field, Engineers Without Borders, has conducted various studies that reflect on the effectiveness and sustainability impacts of different impeller designs across underserved regions. Their findings highlight how advancements in impeller technology have enabled isolated communities to access clean water efficiently, thus improving their quality of life.
Trustworthiness in choosing an impeller wheel manufacturer cannot be overstated, and businesses are advised to rely on accredited suppliers. The thorough vetting of suppliers is essential, as this ensures that the impeller wheels are manufactured following the industry's best practices and standards. This not only guarantees the device's performance and longevity but also mitigates risks associated with operational failures.
It's also pertinent to seek certifications such as ISO 9001 for quality management systems, assuring that the products meet customer and regulatory standards consistently. In this domain, manufacturers with a proven track record of innovative solutions and customer testimonials often signify reliability.
When selecting an impeller wheel, businesses must consider specific application requirements such as the type of fluid, environmental conditions, and desired pressure output. Emphasizing custom solutions tailored to these parameters presents a more efficient operation and cost savings in the long run. An increasing trend is the customization of impeller wheels to meet the unique challenges posed by new-age industrial applications, such as renewable energy systems where sustainability and efficiency are prioritized.
In conclusion, understanding the nuances of an impeller wheel enhances equipment performance and offers businesses a strategic advantage. By blending experience with expertise and ensuring authoritative trust in manufacturers, businesses can harness the full potential of impeller wheels in optimizing their operations. Leveraging modern technology and materials, the impeller wheel continues to play a pivotal role in innovating industrial machinery, setting a foundation for future advancements in fluid dynamics.