CF8 casting, a precise magnesium alloy casting process, has become something of a buzzword in the manufacturing sector, gaining traction for its exceptional properties and wide-ranging applications. For businesses prioritizing lightweight components without sacrificing strength, understanding the unique qualifications of CF8 casting is crucial. Here, we delve into its technical prowess, industry applications, and expert insights to leverage its benefits maximally.
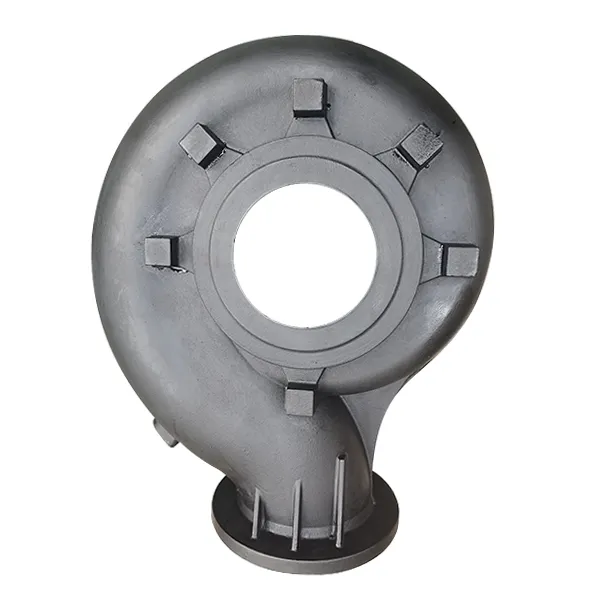
CF8 casting incorporates cutting-edge foundry techniques, which fuse magnesium's lightweight properties with other alloying elements to produce components that are not only robust but also resistant to corrosion and high temperatures. This casting method stands out because of its ability to produce thin-walled, geometrically complex parts that maintain high structural integrity. The precision offered by CF8 casting is unparalleled, allowing manufacturers to create components that meet stringent specifications and industry standards.
The application of CF8 casting is extensive and spans various sectors, making it an authoritative choice for industries like automotive, aerospace, electronics, and telecommunications. In the automotive industry, for instance, the pursuit of fuel efficiency and performance enhancement underscores the demand for lightweight yet strong materials. CF8 casting supports automotive manufacturers in achieving weight reduction in vehicles, contributing directly to improved fuel economy and lesser environmental impact.
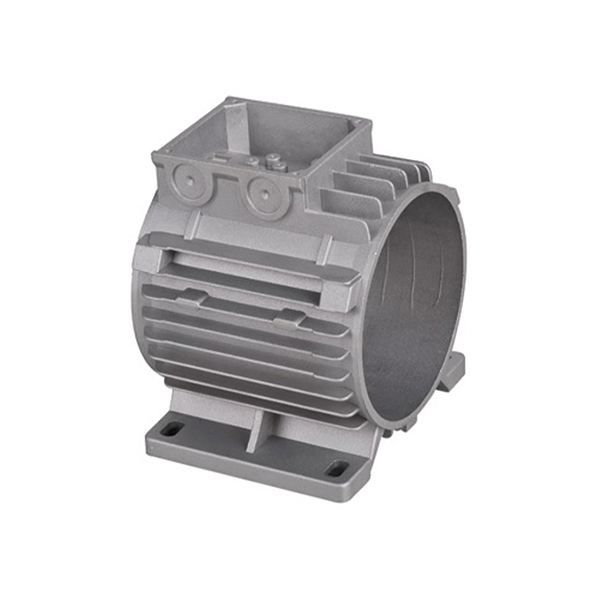
Similarly, the aerospace industry's stringent demands for materials that can withstand extreme conditions make CF8 casting a preferred choice. The lightweight nature of magnesium alloys, without compromising durability and performance, helps in reducing the overall weight of aircraft, leading to better fuel efficiency and an increase in payload capacity. Components made via CF8 casting are valued for their precision, which is crucial in aviation for ensuring safety and reliability.
cf8 casting
Expertise in CF8 casting comes not only from theoretical knowledge but also from hands-on experience and technical prowess. Industry leaders often emphasize the importance of selecting the right magnesium alloy composition based on specific application requirements. They relate experiences of overcoming common challenges such as shrinkage porosity and ensuring consistency in the microstructure. The challenges of CF8 casting are mitigated through rigorous quality control measures, such as real-time monitoring and advanced mold design techniques, ensuring that the final products meet rigorous manufacturing standards.
Authoritativeness in CF8 casting is established through collaboration with research institutions and professional bodies dedicated to advancing foundry technologies. Continuous learning and adaptation are key, as new alloy compositions and casting technologies are developed to push the boundaries of what's possible. Industry conferences and publications serve as platforms for sharing breakthroughs in CF8 casting methodologies, fostering a community committed to innovation and excellence in casting.
Trustworthiness in the CF8 casting field is built through consistent product performance and reliability over time. Manufacturers tapping into CF8 casting must prioritize operational transparency and adherence to international safety and environmental standards. Certification by recognized bodies further establishes credibility, showcasing a commitment to quality and customer satisfaction.
In conclusion, CF8 casting is not merely a method of production but a strategic approach to manufacturing that aligns with global demands for sustainability, efficiency, and innovation. It offers unmatched advantages in terms of component weight,
strength, and design complexity. As industries evolve, embracing CF8 casting positions manufacturers at the forefront of technological advancement, enabling them to craft components that meet the dynamic needs of modern engineering. Adopting CF8 casting demonstrates a commitment to pushing the envelope in material science and engineering, thereby contributing to a future driven by precision, performance, and sustainability.